Digitizing China's rice chain
Inside one of the world’s biggest automated rice seed sites.
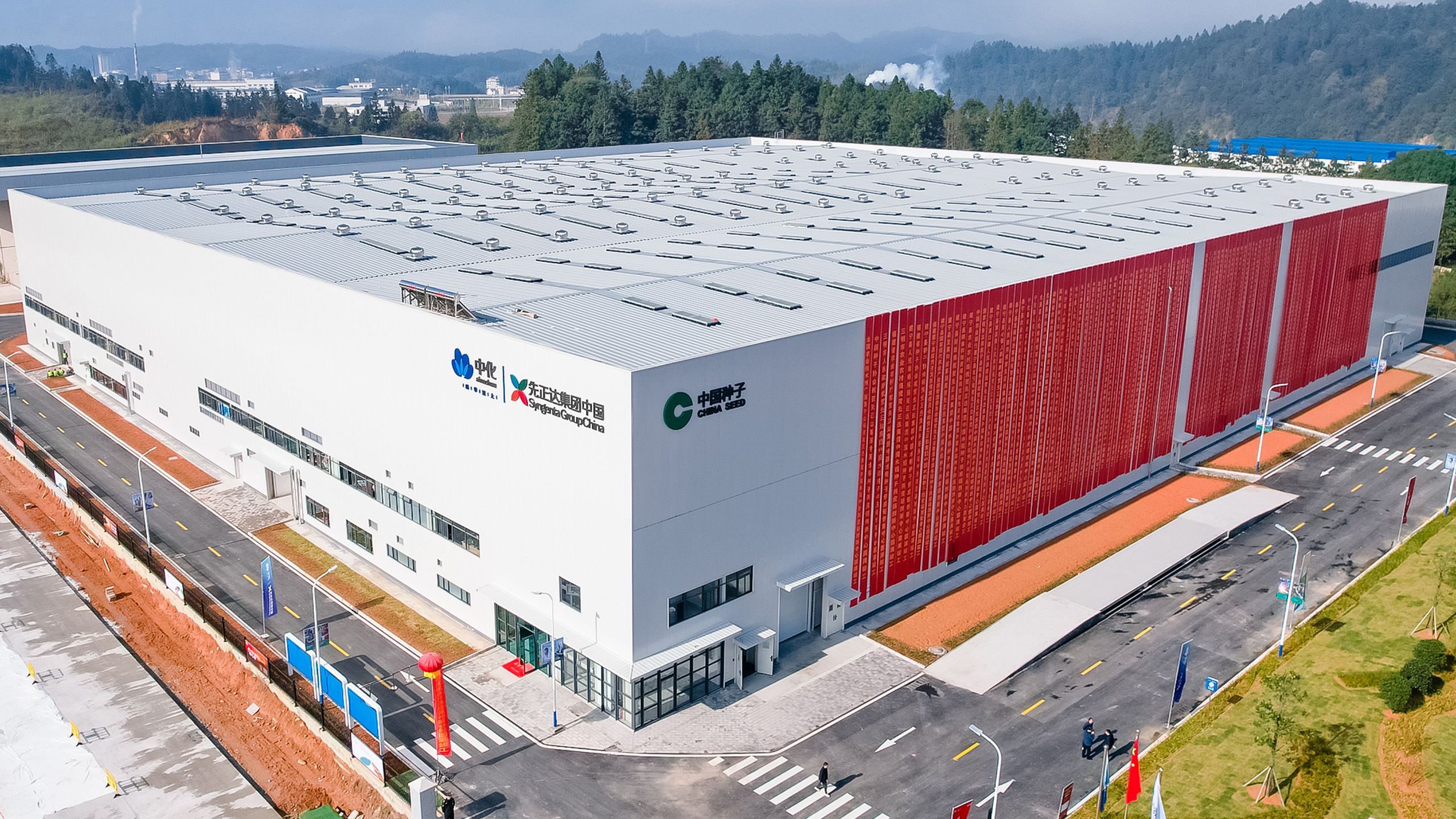
In the heart of China’s Wuyi Mountains, an autonomous giant hums with life.
Twelve identical conveyor belts connect neatly arranged packaging lines where an endless supply of small packages glide along orderly lanes that snake along the factory floor.
In this factory, the workers’ movements are precise, efficient and tireless. Their robotic arms grab, rotate and deliver the packages to their handlers whose wheels carry the seeds to their next destination.
Only eight people work here during the busy season – the rest of the day-to-day tasks at this Jianning processing plant are carried out by autonomous machines with such efficiency that the factory appears to run itself.
But it wasn’t always like this. Historically, the Syngenta seeds grown in this region were transported to a network of processing sites more than 350 kilometers away.
It was organized but inefficient, says Kun Hao, Head of Syngenta Group China’s Rice Business.
“The processing efficiency was low and most of the work was done manually,” he says.
Nevertheless, these sites processed a near-unfathomable number of seeds each year. In total, 3,000 tons of rice seeds were processed and packaged every year. Imagine 20 blue whales lined up in a row and you’ll come close to the average annual weight.
Even with these enormous volumes, it wasn’t enough. With global rice production forecast to reach 636 million tons by 2030, a dramatic boost in production was essential.
All eyes turned to automation. Could this close the gap between how much the sites could process and how much was needed?
It was something the industry was well behind on, Hao explains. “Compared with many other industries, the degree of automation, informatization and intelligence in agriculture, especially in the rice processing industry, is still relatively low.”
Syngenta's autonomous factory in Jianning, China can process 10,000 tons of rice seed every year.
Syngenta's autonomous factory in Jianning, China can process 10,000 tons of rice seed every year.
New technology for a new world
Until last year, the rice seeds at Syngenta’s site in the Wuyi Mountains underwent a series of complex, labor-intensive processes before sale. It was here, in the space between harvesting and distribution, where most of the work was done by hand, that the chain started to fragment.
Everything changed last November. Syngenta’s new behemoth site opened, joining these disparate processes into a single straight line, forming a “rice road” for seed processing.
For the first time, these elements - drying, fumigation, conditioning, seed treatment, bagging and storing – all happened on one site. That meant that the supply of processed rice seed met the ever-increasing demand.
Today, the plant’s processing efficiency is triple that of a traditional seed processing plant, with less than a quarter of the staff. And that means farmers receive their rice seeds to grow faster than before.
"It can process an increased capacity of 10,000 tons of rice seed in a year, meeting the demands of our customers in time,” Hao says. This is the equivalent of 145 tons of rice seed in a single shift.
The factory is entering its peak season. From September to December, it runs eight hours a day, seven days a week, tirelessly cranking out seed packages for distribution.
The global picture
China is the world’s largest rice producer. But the region of Jianning County in Fujian Province on the country’s southeastern coast has long been linked to hybrid rice seed, an innovation credited with saving millions of people from the brink of starvation. The hybrid, first developed in the 1970s, produces yields up to a third higher than non-hybrid strains, or open pollinators, and is more resilient to pests and diseases.
Today, these hybrids are grown on more than 14 million hectares across the country each year. It feeds a further 70 million people annually, shoring up China’s food security. And one of every 10 of those hybrid rice seeds is produced in Jianning where the Syngenta plant is located.
“In the future, most of the work for rice seed production in the fields and in processing will be done by machines,” Hao says of the industry’s expected shift towards more intensive automation.
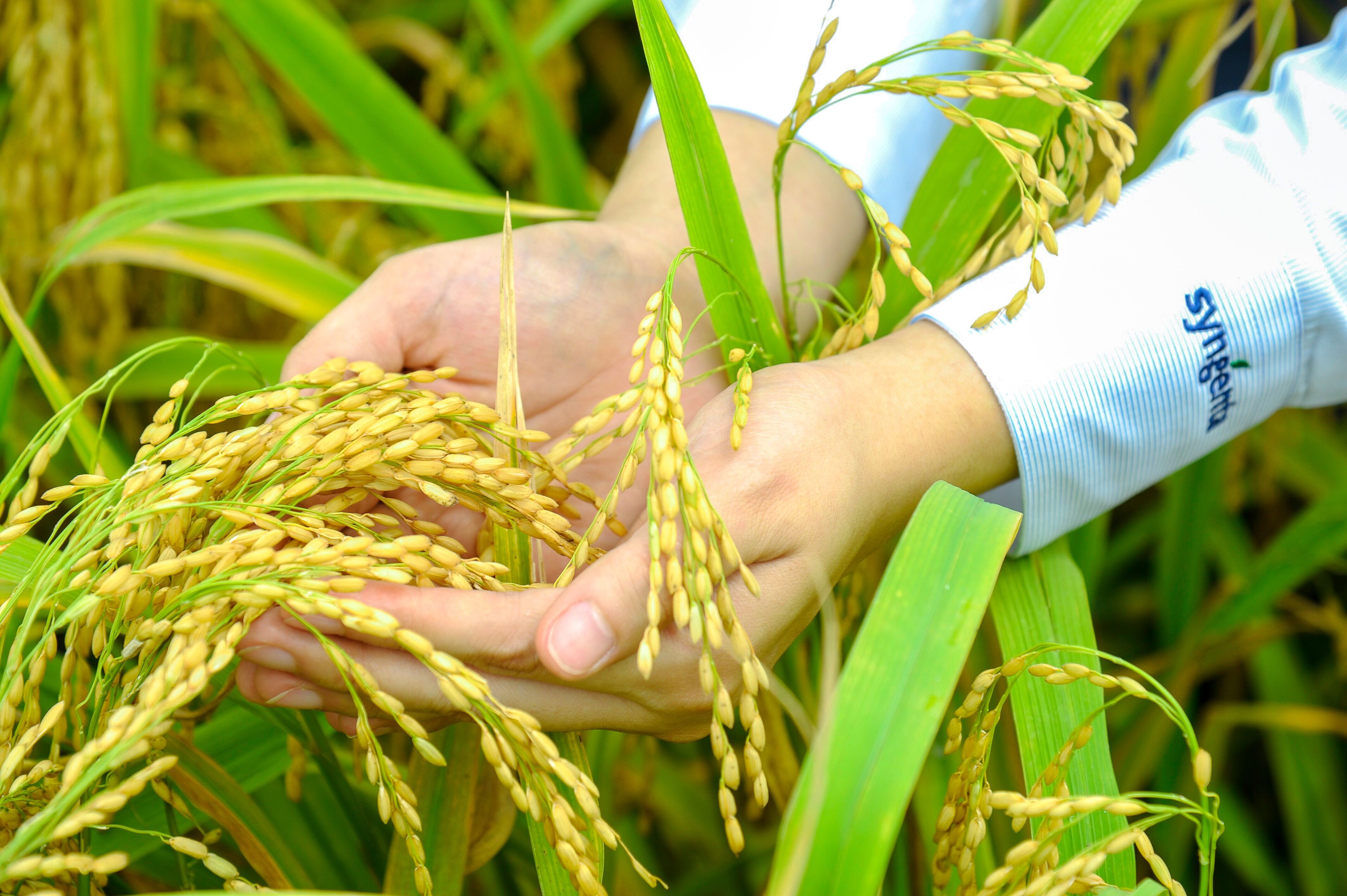
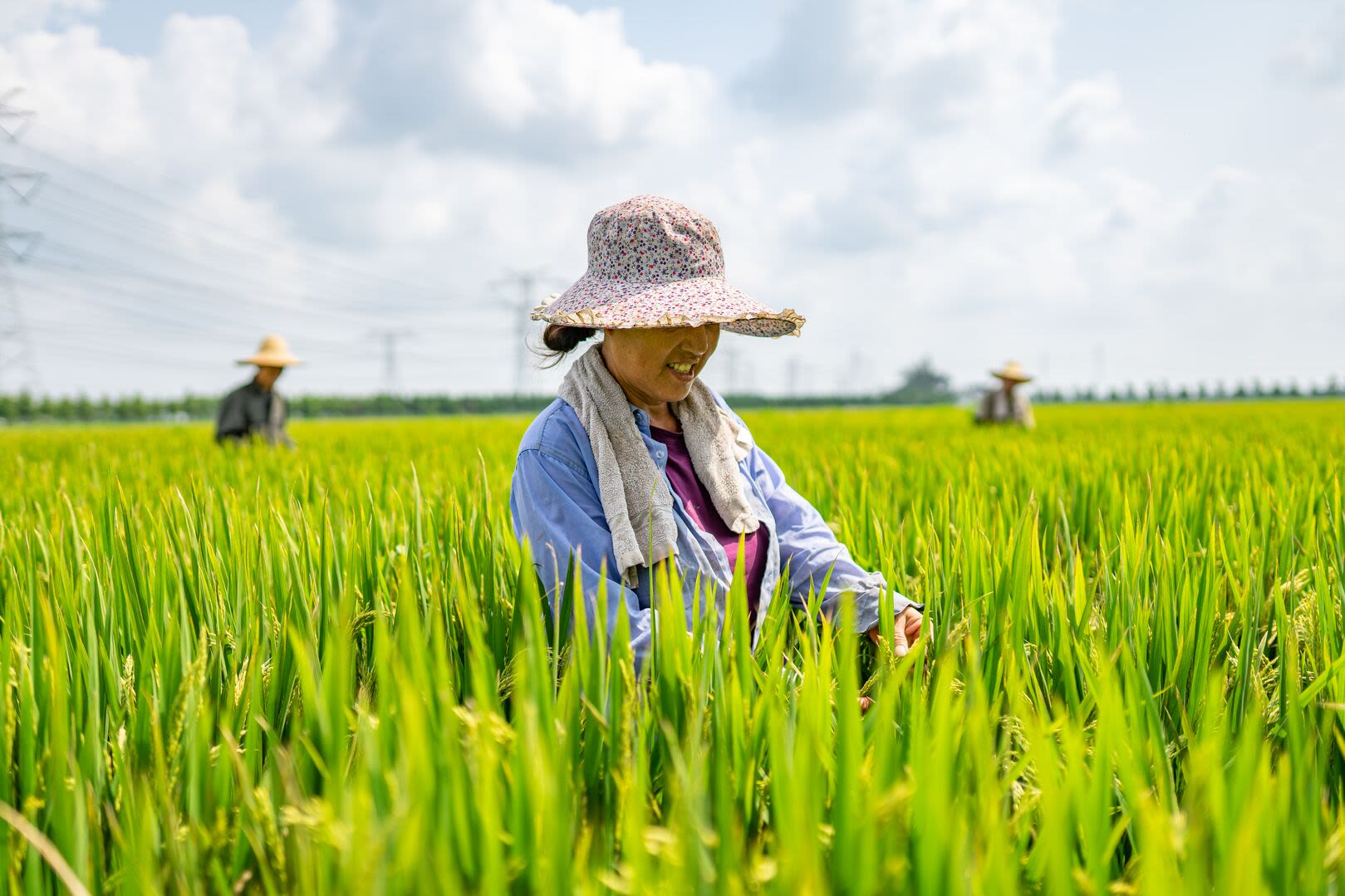
Autonomous efficiencies
But what is rice seed processing? What we think of as something relatively simple is actually a number of stages designed to make rice seed ready to plant by growers.
The rice that arrives at the Syngenta plant undergoes a series of changes before it leaves. The seeds are unloaded, dried, fumigated, conditioned and subject to numerous quality tests before they are packaged and transported to farmers and distributors.
But it’s not just one single innovation or machine at this factory that is responsible for the increased output. At every stage of production, each process has been optimized to make it one of the most advanced and automated rice seed processing plants in China.
Of the eight people who work at the plant, there are two forklift drivers and six seasonal employees who monitor the many machines carrying out the day-to-day functions.
Such is the level of automation that the packaging process – typically the most labor-intensive of all the stages involved – is fully automated, with just two workers keeping an eye on the 12 efficient assembly lines.
Yang Yongjian, Head of the Jianning Factory, says that the packaging and palletizing system is fully automatic by design.
"In this factory, each process section is efficiently connected by an automatic conveyor belt, which effectively solves the problem of the processing steps being separated in traditional plants.”
Only eight people work at the Syngenta factory in Jianning, China - the rest of the day-to-day tasks are carried out by machines.
Only eight people work at the Syngenta factory in Jianning, China - the rest of the day-to-day tasks are carried out by machines.
A central control system oversees each process section and the intelligent use of autonomous machines: hydraulic unloading platforms, automatic packaging and palletizing systems, autonomous guided vehicles and vertical warehouses mean that the day-to-day work of the site has been reimagined and futureproofed.
The integration of so many moving parts wasn’t seamless, however. If one section doesn’t function as it should, it skews the whole pipeline. Yongjian says that this is a quirk of the factory’s autonomous design.
"High automation has brought higher challenges to the stability and smoothness of the entire process.
“We are the first to try it out. There is no ready-made experience to follow. We can only rely on ourselves to explore step by step."
Forging ahead
It is fitting that this innovative factory also houses a first-of-its-kind patented circulation fumigation technology. This eliminates pests and harmful organisms from the seeds, making them safe for storage.
Yongjian explains that the innovative design of the plant’s process saves time and is more sustainable than traditional methods. The seeds are then transported to the fumigation warehouse by an autonomous guided vehicle.
“The time is greatly shortened compared to traditional fumigation, from the original 10-14 days down to five to seven days, thanks to this design.
“After the fumigation is completed, the exhaust gas is discharged after harmless purification, without the need for human intervention, which is safer, healthier and more environmentally friendly."
In line with this innovative approach, the conditioning process - during which seeds that don’t pass muster are weeded out - has also been optimized.
Specialized equipment tests the quality of each seed lot, such as its moisture content, weight and purity.
The machinery is so precise that it can 'jump' some conditioning steps at will, according to the seeds’ characteristics and quality, ensuring efficiency.
"If the appearance and color of the seeds are good, you can skip the other steps and go directly to the next link to improve the conditioning efficiency,” Yongjian says.
Only the seeds that pass another round of quality tests will make it to packaging.
The seeds must pass several rounds of quality testing before they are packaged.
The seeds must pass several rounds of quality testing before they are packaged.
"Precision conditioning equipment and strict testing systems improve the screening accuracy and ensure the objectivity of seed quality assurance,” Yongjian says. “They ensure that every seed lot coming off the processing line is of high quality.”
For these seeds, the journey isn’t over. After packaging, they leave Jianning for the first time and make their way to farmers and retailers across China and further afield, using well-oiled networks that transport one of world’s most important foods.
Furthermore, processing these seeds in their local region strengthens the rice seed chain in China, futureproofing this global crop. That’s why, according to Hao, the biggest advantage of this new factory is its 'foresight'.
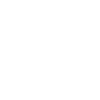