数字化赋能中国水稻产业链
探秘全球顶尖的水稻种子供应链创新中心。
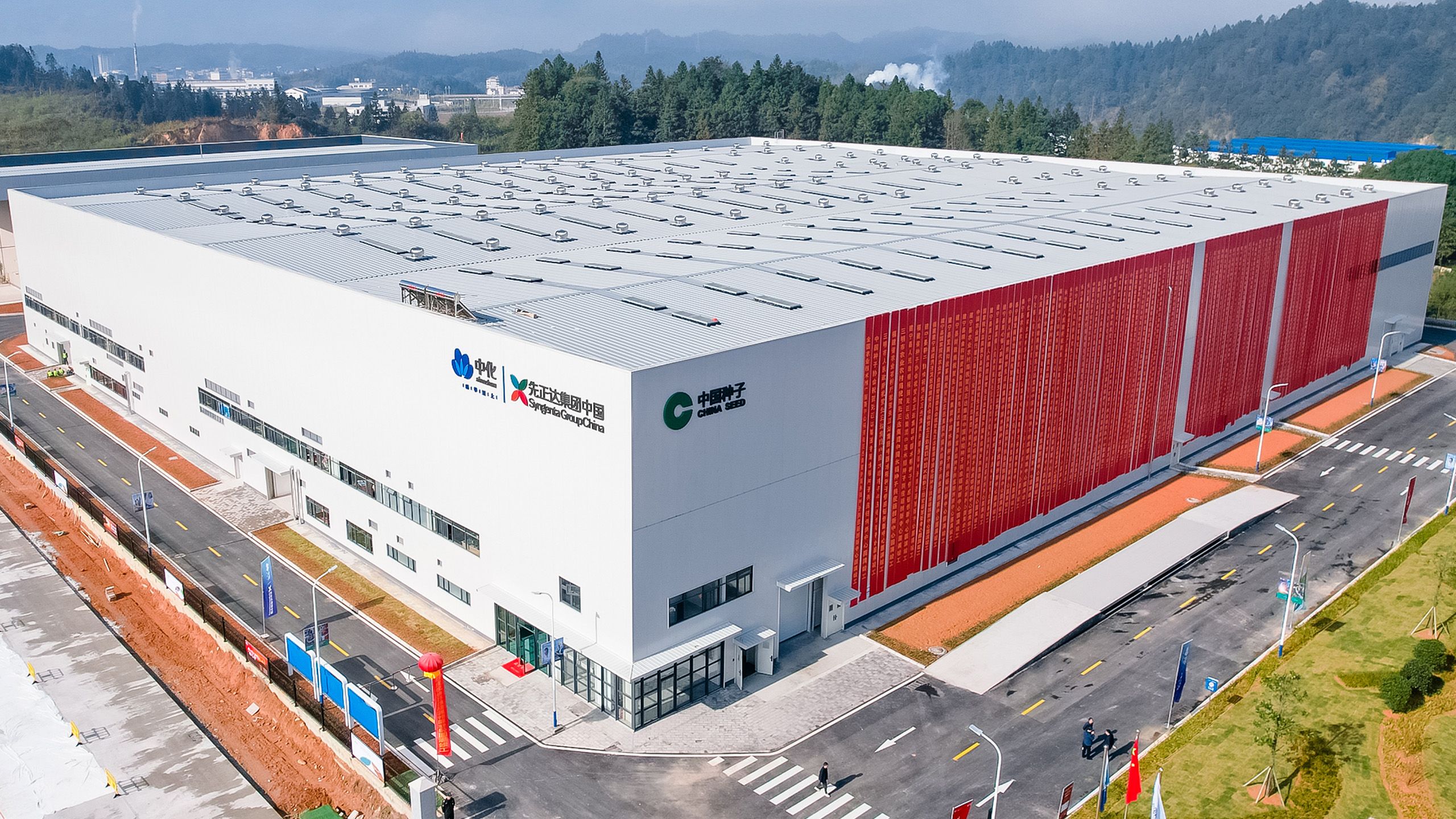
在中国武夷山脉中段,一座自动化超级工厂的机器正轰鸣忙碌着。
12条相同的传输带,连着排列整齐的包装流水线。在这里,体积小巧的包装成品源源不断地沿着地面上蜿蜒的传输带匀速前进。
在建宁工厂“工人们”的动作精准而高效,不知疲倦。经过机械臂抓取、转动及搬运等一系列操作,将成品递送给自动导向车,后者的轮子转动,再将种子送至下一目的地。
即使在旺季,建宁工厂也仅配备8名员工——其他日常运营任务均由自动化设备高效完成,仿佛工厂在自行运作。
但以前并非如此。曾经,该地区收获的先正达种子需要长途跋涉350多公里,才能到达各加工厂。
先正达集团中国水稻业务负责人郝琨表示,尽管流程运行有序,但效率并不理想。
“我们过去的加工效率相当低下,”郝琨回忆道,“大部分工作依赖于人工操作。”
尽管如此,这些工厂每年处理的种子数量之巨,几乎难以想象。据统计,每年加工和包装高达3000吨的水稻种子。打个比方,这相当于20头蓝鲸横亘在你面前。
数量如此巨大,仍不足以满足未来的需求。预测到2030年全球水稻产量将达到6.36亿吨。因此,大幅提升产量变得尤为迫切。
在此背景下,自动化技术成为了众人瞩目的焦点。它能否弥合现有加工能力与需求之间的巨大鸿沟?
郝琨解释道,在这方面,整个行业都还有很长的路要走。“与其他许多行业相比,农业,尤其是水稻种子加工行业的自动化、信息化和智能化水平,目前还相对较低。”
先正达位于中国建宁的自动化工厂,每年能够加工高达1万吨的水稻种子。
先正达位于中国建宁的自动化工厂,每年能够加工高达1万吨的水稻种子。
面向新世界的新技术
直至去年,先正达的武夷山基地在销售前还需对水稻种子进行一系列繁琐且耗费人力的处理流程。收获与销售之间的大部分工作依赖人工操作,导致整个供应链效率不高。
然而,去年11月,一切都变了。先正达新建的超级工厂正式启用,将这些分割条块整合起来,形成一条高效的种子加工新“稻”路。
烘干、环流熏蒸、精选、包装和仓储等全流程工段首次可以在同一工厂完成,确保了加工的水稻种子供应量能够跟上不断增长的市场需求。
如今,该工厂的处理效率是传统种子加工厂的三倍,员工数量却不到以往的四分之一。因此,农民能以更快速度获得他们所需的种子。
郝琨表示:“该工厂现在每年可以处理高达1万吨的水稻种子,确保及时满足客户的需求。”这相当于每个班次能处理145吨水稻种子。
这家工厂即将进入生产旺季。从9月到12月,每周7天,每天8小时火力全开,充分备货。
全球形势
中国是世界上最大的水稻生产国,而位于东南沿海的福建省建宁县更是因其杂交水稻种子而闻名遐迩,这一创新曾拯救了数以百万计处于饥饿边缘的人们。这一杂交品种20世纪70年代首次培育成功,其产量可比非杂交品种或开放授粉品种高出三分之一,同时更能抵御病虫害的侵袭。
如今,超过1400万公顷的土地上种植着此类杂交品种,每年另为7000万人提供粮食,夯实了中国的粮食安全。而每10粒杂交水稻种子中,就有一粒诞生于建宁——先正达工厂的所在地。
“展望未来,田间的水稻种子生产和加工的大部分工作都将由机器完成,”针对该行业进一步向高度自动化转型的趋势,郝琨如是说。
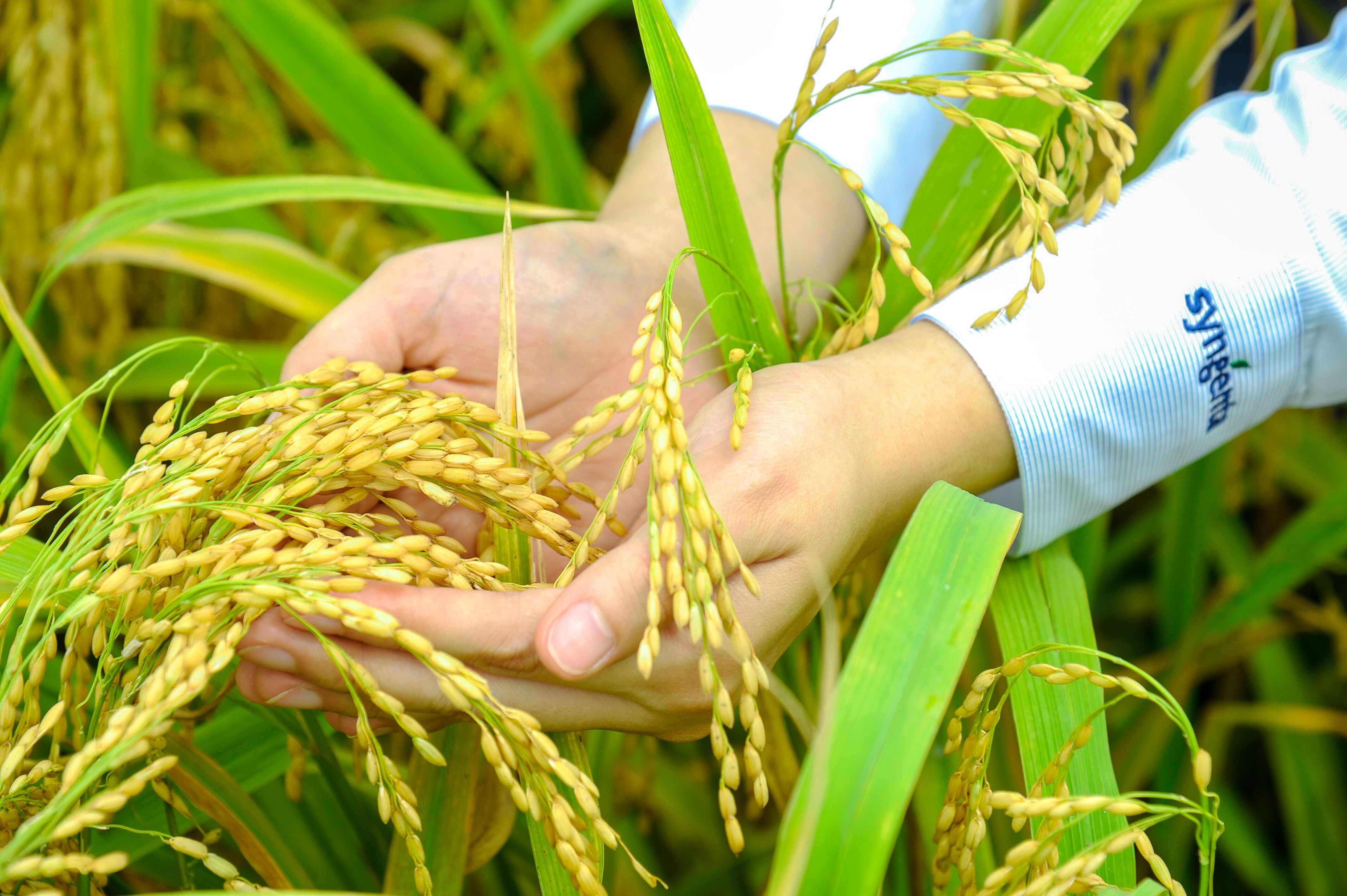
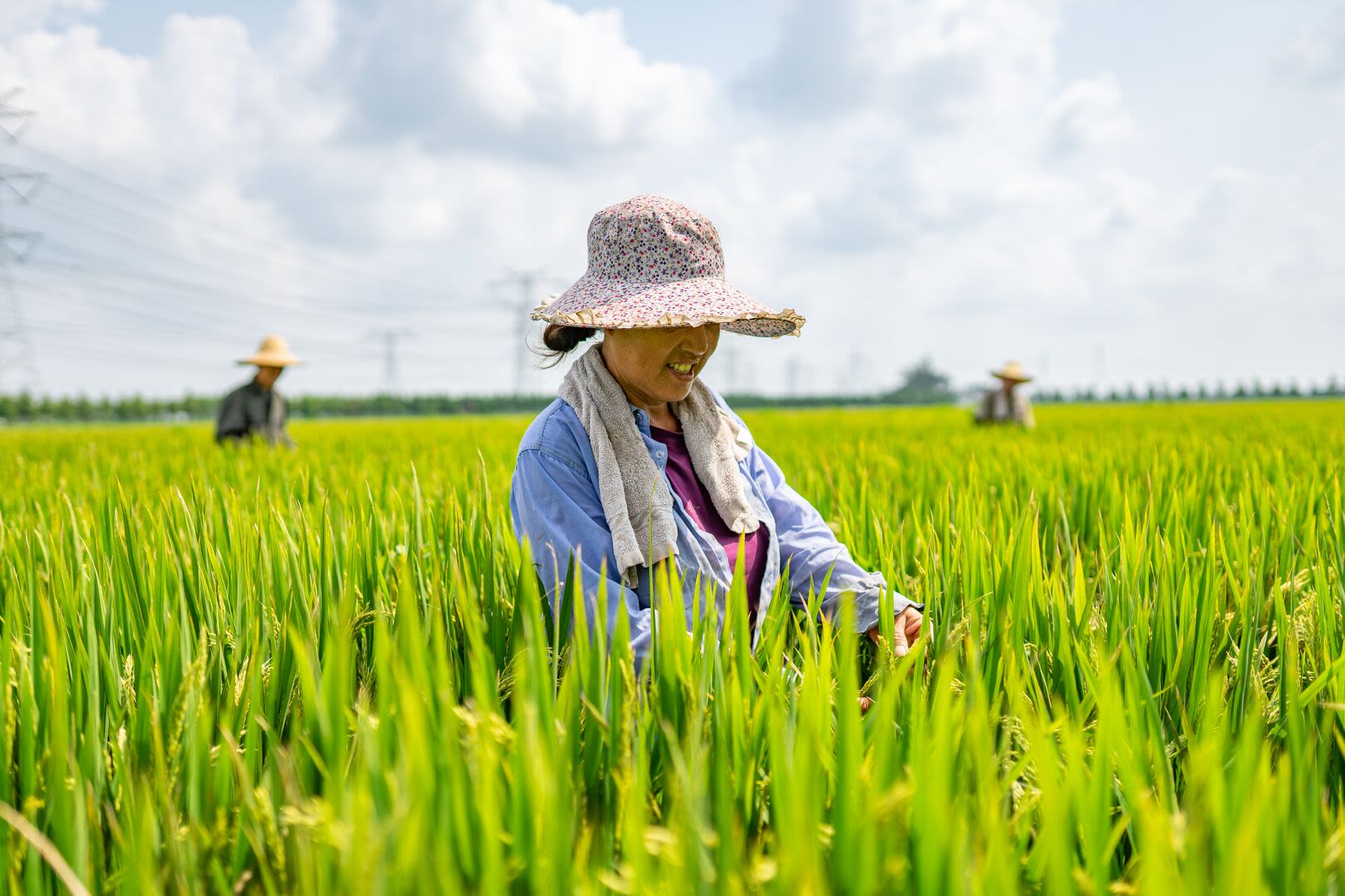
自动化效率
什么是水稻制种?这一过程看似简单,实际上包含多个工段,旨在为种植者提供优良的种子。
水稻种子抵达先正达工厂后,在出厂前会经历一系列加工。它们经过卸料、烘干、熏蒸、精选,以及无数次质量检测,才能进行包装并运送至农民和分销商手中。
然而,这家工厂能够提高产量,并非仅依赖单一的创新或设备。每个工段的每个步骤都经过了优化,使其成为全中国最先进、自动化程度最高的水稻种子加工工厂之一。
工厂的8名工作人员各司其职,其中2名叉车操作员以及6名负责监控众多机器运作的季节性员工。
这里的自动化程度极高,连包装流程——通常被认为是整个生产环节中最耗费人力的部分——也实现了全自动化,仅需2名员工即可轻松监管12条高效的流水线。
建宁工厂负责人杨永坚指出,工厂的包装和码垛系统是按照全自动化的理念设计的。
“在建宁工厂,各工段之间由自动传输带高效衔接,有效破解了传统水稻种子加工条块分隔、无法有效衔接的难题。”
这个工厂仅需8名员工,而其他所有日常工作都交由自动化设备完成。
这个工厂仅需8名员工,而其他所有日常工作都交由自动化设备完成。
通过中央控制系统对主要工段进行操控,并引入自动液压装卸货平台、自动包装和码垛系统、智能仓储管理系统、物流信息管理系统、自动导向车等自动化设备和技术,这意味着该工厂的日常运作已经重构,可适应未来的发展趋势。
然而,将如此众多的动态部件整合在一起并非易事。全模块、全流程的自动化,意味着其中任何一个环节出问题,其他工段都会跟着受影响。杨永坚指出,这是工厂自动化设计面临的难题。
“高度自动化对全流程工艺的稳定性和通畅性带来了更高挑战”
我们是第一个‘吃螃蟹的人’,没有现成的经验可循,只能靠自己一点一点摸索。”
开拓进取
环流熏蒸是建宁工厂拥有的一项专利技术,系全球首创,极具创新。该技术能够彻底清除种子中的害虫和有害生物,确保种子的安全储存。
杨永坚解释说,工厂的创新工艺设计不仅节省了时间,而且相比传统方法更具可持续性。种子由自动导向车运送到密闭环流熏蒸仓中。
“得益于这一设计,熏蒸时间从传统的10-14天大幅缩短至5-7天。”
“熏蒸完成后,尾气经过无害净化处理排出,无需人工介入,更加安全健康环保。”
与这种创新方法相一致,种子的精选工艺——即筛选剔除不合格种子的环节——也经过了改良。
专业设备会对每一批次的种子进行质量检测,测定它们的水分、重量和纯度。
这些设备的精准度极高,能够根据种子的特性和质量灵活“跳过”某些精选步骤,从而确保效率。
杨永坚介绍:“如果种子的外形、颜色都比较好,就可以跳过色选或其他的步骤,直接进入下一环节,提高精选效率。”
“重重考验”的种子才是真正质量合格的种子,才能进行下一步的包装。
种子在包装之前,必须经历一系列严格的质量检测流程。
种子在包装之前,必须经历一系列严格的质量检测流程。
“精密的精选设备和检测仪器,有助于提高筛选精准度,也能确保种子质量评定的客观性。保证从加工线下来的种子粒粒是精品。”,杨永坚表示。
此时,这些种子的旅程才尚未结束。包装完成后,它们首次告别建宁,借助高效运转的物流网络,前往中国各地乃至更远的农民和零售商手中——这些网络是运输世界上最重要粮食之一的纽带。
此外,在当地加工种子,不仅加强了中国水稻种子供应链的韧性,也为这种全球性作物的未来发展提供了保障。郝琨认为,这家新工厂的最大优势在于其“前瞻性”。
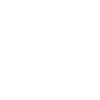